AI-Powered Direct Quality Feedback Solution for Škoda Auto
Improving the efficiency and accuracy of error detection on the production line.
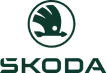
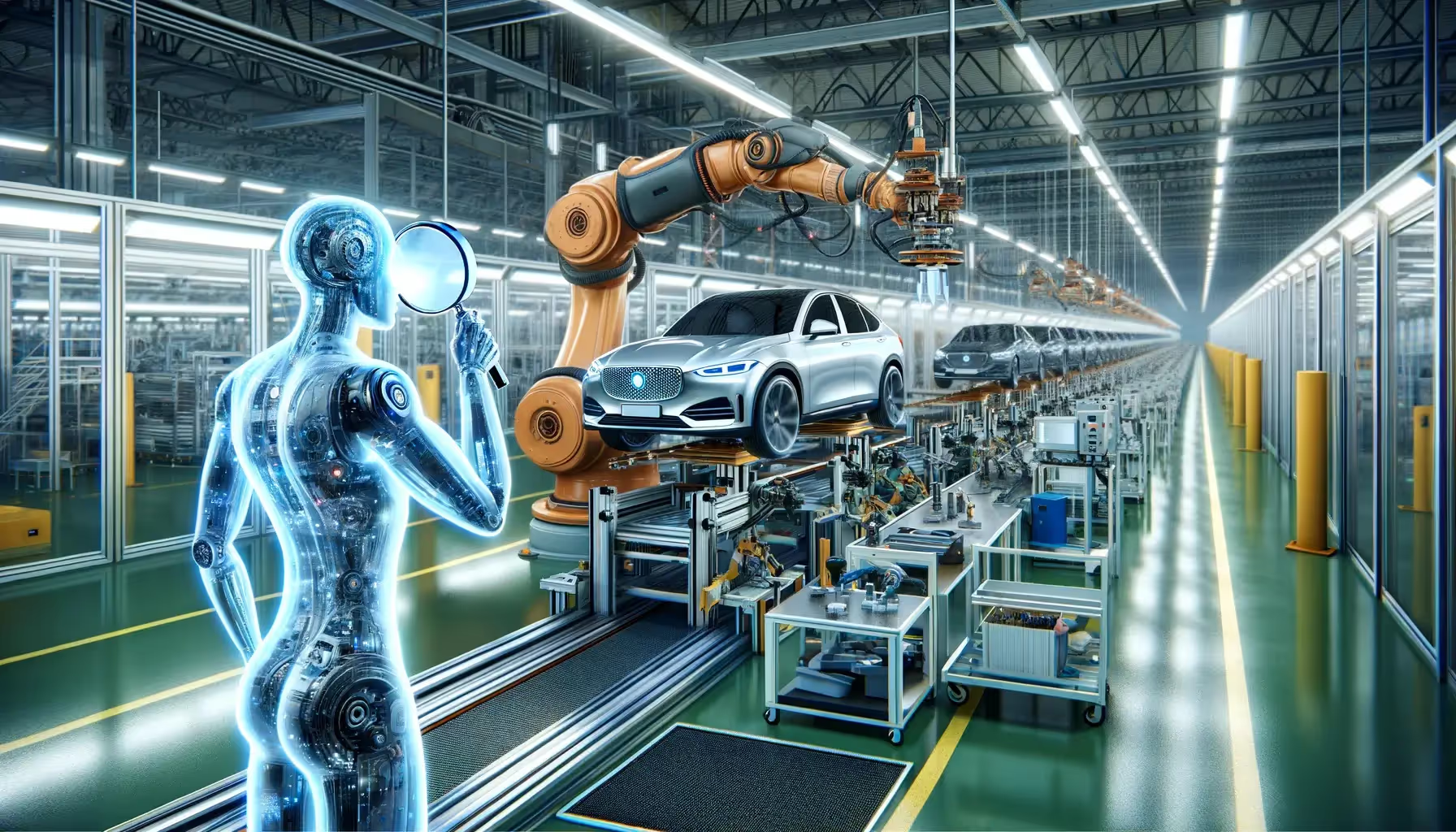
Project Overview
The purpose of the Direct Quality Feedback (DQF) project at Škoda Auto was to enhance the process and hasten feedback in identifying errors on the production line at the Kvasiny plant, Czech Republic (and later at other sites).
Before, when an error was found in the manufacturing process, the responsible worker had to document the defect and then manually track back to figure out at which production operation the error happened, who was working at that time, and which worker was responsible for the mistake.
By speeding up the detection of errors in the manufacturing process using AI, workers receive feedback more promptly and the frequency of errors is reduced. Consequently, the DQF ultimately increased the speed of car production on the line.
Highlights of the Collaboration
- The AI-powered solution in the core
- Ability to detect more than 85% of defects and assign it to a specific operation
- The ROI exceeds 230%
Project Challenges and Objectives
Provided Solution
The AI-Powered Solution
When developing the AI solution, we realized that the traditional "pre-trained" language models lacked domain knowledge. So we had to create a multi-step solution, first performing language preprocessing using classical statistical methods.
This made it possible for the neural network to learn much faster, gradually reducing the amount of training data needed. Through these steps, we were able to achieve the required accuracy for the entire solution.
[.dlazdice][.karta][.nadpis]Experiments[.nadpis][.radek]Testing methods and approaches, integrating them, and determining which solution will be effective.[.radek][.karta][.karta][.nadpis]Validation of Success[.nadpis][.radek]Gradually training the model based on client feedback, allowing the model to learn and improve.[.radek][.karta][.karta][.nadpis]Development, Integration & Deployment[.nadpis][.radek]The actual development of the DQF application and the integration of AI solutions with other production systems at Škoda Auto Kvasiny.[.radek][.karta][.karta][.nadpis]Improvement & Learning [.nadpis][.radek]Within the MLOps framework, we are capable of real-time "retraining" of the model for new car models, equipment levels, or manufacturing processes.[.radek][.karta][.dlazdice]
Results
The main prerequisites for the successful implementation of our solution were the digitalization of most production systems, the integration of databases, and the identification of the number of defects and their combinations (over 12 million possibilities).
Scaling the Succesful Use of AI
Thanks to the new DQF application, Škoda Auto is able to detect and assign more than 85% of defects to a specific operation and place of origin. This saves time in identifying errors and locating the workstation, increases production efficiency, and improves communication between workers, as well as accelerates their training. Additionally, DQF reduces the workload on shift supervisors in the plants.
The return on investment (ROI) in time savings and production process improvement exceeds 230%. The goal is also to roll out the final solution to other facilities and continue expanding it to include various equipment levels (optional/extras, additional models, etc.).
Let’s make something great
We are here to help you.